Understanding LEV Inspection in South Wales
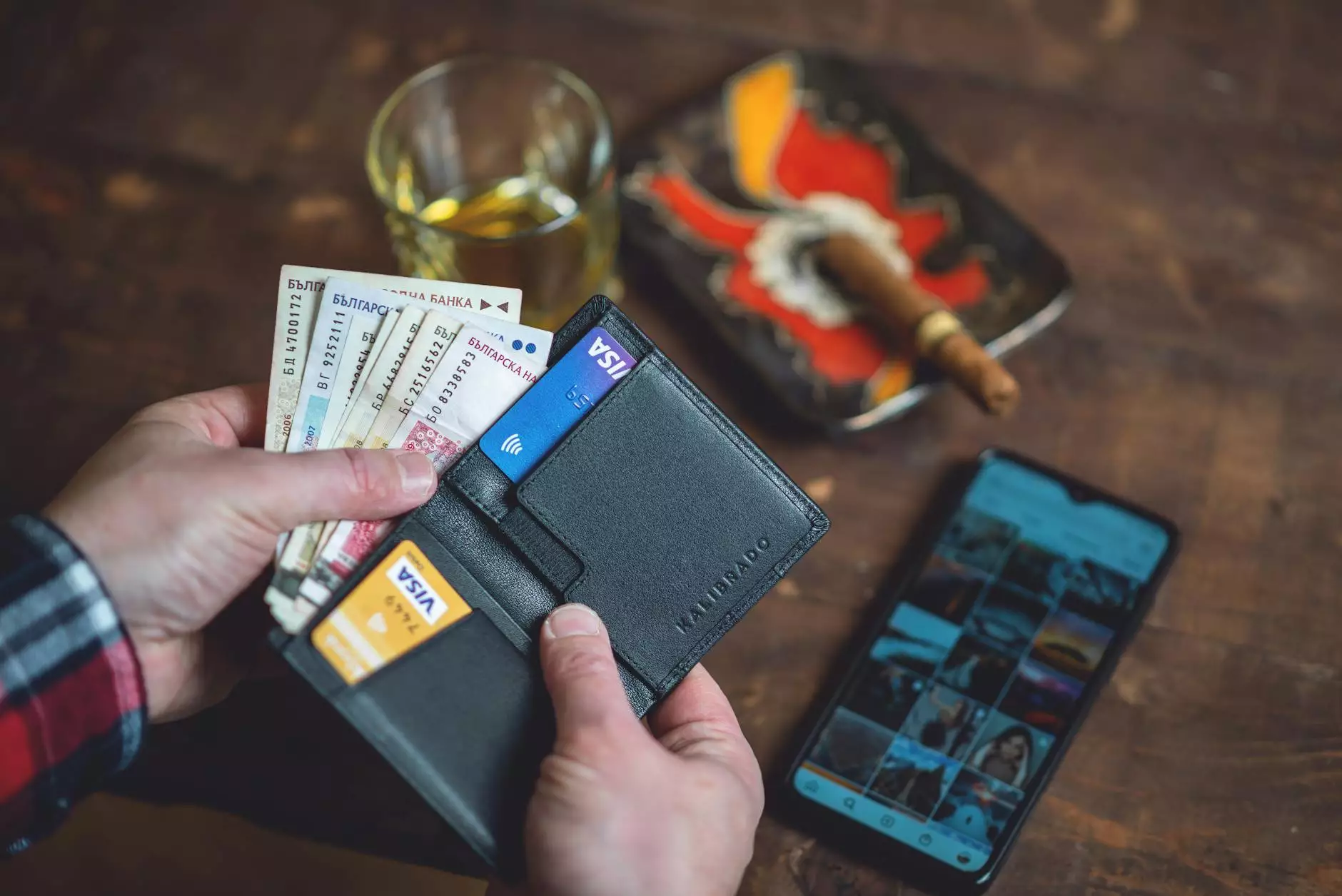
Local Exhaust Ventilation (LEV) systems are crucial for businesses that handle hazardous substances. They help protect workers and the environment by minimizing exposure to harmful particles and fumes. In South Wales, the necessity for LEV inspection is not just a regulatory requirement but a significant aspect of workplace safety and health compliance.
What is LEV Inspection?
LEV inspection is a thorough examination of ventilation systems designed to capture and filter airborne contaminants at their source. By effectively removing hazardous substances from the workplace, these systems play an essential role in promoting a safe working environment.
Why is LEV Inspection Crucial for Businesses?
Conducting regular LEV inspections is vital for several reasons:
- Compliance with Regulations: Businesses in South Wales must adhere to specific legal requirements regarding air quality and worker safety.
- Health Protection: Regular inspections help prevent respiratory illnesses and other health issues among employees.
- Operational Efficiency: Well-maintained LEV systems function more effectively, conserving energy and reducing operational costs.
- Reputation Management: Demonstrating a commitment to employee safety can enhance a company’s reputation and attract talent.
Key Components of LEV Systems
Understanding the components of LEV systems can help businesses ensure their effectiveness:
- Extraction Arms: Designed to capture pollutants at their source.
- Hoods: These are the openings through which airborne contaminants are drawn into the system.
- Ductwork: Transports contaminated air to filters or other treatment systems.
- Filters: Remove particulates and contaminants from the air before it is recirculated or released.
- Fans: Create the necessary airflow to move contaminants through the system.
The LEV Inspection Process
The LEV inspection process involves several key steps:
- Pre-Inspection Preparation: Gathering relevant system documents and previous inspection reports.
- Visual Inspection: Examining the entire LEV system for signs of damage, wear, or incorrect installation.
- Performance Testing: Measuring airflow and assessing the system's efficacy in removing contaminants.
- Documentation: Compiling a report detailing findings, maintenance needs, and compliance status.
- Follow-Up Recommendations: Providing actionable steps for any necessary repairs or improvements.
Regulatory Framework for LEV in South Wales
In South Wales, companies must comply with national regulations governing laboratory and industrial practices, specifically regarding air quality and worker protection. The key regulatory bodies involved include:
- Health and Safety Executive (HSE): Offers guidelines and frameworks for air quality management.
- Control of Substances Hazardous to Health (COSHH): Regulates the handling of hazardous substances.
- Local Authorities: Implement local environmental health policies that impact LEV requirements.
Best Practices for Effective LEV Inspection
To ensure comprehensive and effective LEV inspections, businesses should adopt best practices:
- Regular Schedule: Establish a routine inspection schedule to ensure ongoing compliance and safety.
- Professional Technicians: Utilize experienced professionals to perform inspections and maintenance.
- Employee Training: Train employees on recognizing LEV system issues and the importance of reporting them.
- Documentation Maintenance: Keep accurate records of inspections, maintenance, and any remedial actions taken.
The Impact of Poor LEV Management
Neglecting LEV inspections can lead to significant issues for businesses, including:
- Health Risks: Increased exposure to harmful substances can lead to serious health consequences for employees.
- Legal Consequences: Failing to comply with regulations can result in fines and legal action.
- Decreased Productivity: Health issues and system inefficiencies can negatively affect employee productivity.
- Reputation Damage: Non-compliance and unsafe practices can harm a company's reputation and credibility.
Choosing the Right LEV Inspection Service in South Wales
When selecting a service for LEV inspection in South Wales, consider the following factors:
- Certifications and Qualifications: Ensure that the service provider is accredited and has qualified personnel.
- Experience: Look for a company with a proven track record in LEV systems and inspections.
- Comprehensive Services: Choose a provider that offers complete inspection and maintenance services.
- Customer Reviews: Check testimonials and reviews to assess the quality of their services.
Common Myths About LEV Inspection
Several misconceptions about LEV inspections can lead to misunderstandings:
- Myth 1: “LEV systems do not require frequent inspections.”
- Myth 2: “All LEV systems are the same.”
- Myth 3: “Hiring professionals is unnecessary for small businesses.”
Dispelling these myths is important for ensuring that all businesses take the proper precautions to maintain safe working conditions.
Conclusion
In conclusion, LEV inspection in South Wales is an essential element of workplace safety and compliance. Businesses must prioritizetheir LEV systems to protect their employees and adhere to regulations. By understanding the importance of regular inspections, choosing reputable service providers, and implementing best practices, companies can effectively manage their LEV systems and minimize health risks. For more information on how Safe Plant UK can assist with your LEV inspection needs, visit Safe Plant UK.
Contact Us for Your LEV Inspection Needs
For businesses in need of LEV inspection services in South Wales, Safe Plant UK offers expert solutions tailored to your specific requirements. Our experienced professionals are dedicated to maintaining the safety and efficiency of your workplace.
lev inspection south wales